The focus of the visit was to explore the innovative solutions that have emerged in response to the climate and biodiversity crisis and their potential to address the decarbonisation challenges in the construction industry. Alongside the positive developments, Ian also highlights some concerns and areas that require further exploration.
Associate Ian Poole from our Sustainability team shares his firsthand experience and observations from a recent visit to the Holcim Innovation Centre.
The Positives
Cement can be reused by recovering and re-separating constituents from concrete waste, reducing the need for new clinker production. Additionally, this process can provide higher quality aggregates replacing new aggregate extraction without requiring additional water and cement. While this approach requires additional energy, cost, and equipment, the benefits of upcycling outweigh these challenges.
These supplementary cementitious materials (SCMs) can partially replace Portland cement in mixes (typically up to 50% replacement), an opportunity to significantly reduce Portland cement demand. This will also help in replacing materials like GGBS and fly ash as they become unavailable due to phasing out of fossil fuels. The abundance of calcined clays and limestone fines, and the use of waste heat recovery for calcining clays makes these materials both commercially viable and low carbon. If used together (e.g. LC3), these constituents are very efficient, forming durable and high strength concrete - many codes already allow this specification (although the UK doesn’t).
With its potential to enhance the strength and durability of concrete when combined with certain cements, graphene offers opportunities for reducing concrete quantities and reinforcement requirements. Promising initial applications appear to be lightly reinforced slabs (e.g., grade slabs and metal decks). However, challenges remain, such as ensuring the even distribution of graphene nanomaterial in the mixes to avoid weak spots in the concrete – just 100g of graphene is used per m3 of concrete (0.00005% by mass).
Holcim anticipates that Carbon Capture, Utilisation, and Storage (CCUS) will become cheaper than the carbon taxes imposed by ETS by 2035. This shift creates an incentive to decarbonise or to develop CCUS capacity. The downside of relying on CCUS is that it increases the cost of cement by £150/tn, which would increase the cost of concrete. This could in turn shift the dial towards material retention, reduction, and substitution, which is arguably crucial for a regenerative future.
As an alternative to traditional CCUS, technologies are in development which use olivine to sequester the carbon emissions from the production of Portland cement whilst creating a new SCM. The process creates a silica based SCM (similar to fly ash) to supplement Portland cement in a mix and a bi-product magnesium carbonate, an inert and mineralised form of carbon dioxide. In the right proportions, this technology could be a genuinely zero carbon concrete. However, this is still in the very early trial stages.
Although promoted as zero-carbon solutions, AACMs have a higher carbon footprint than Portland cement and rely on high proportions of GGBS, which isn’t sustainably available. Additionally, they require a much larger quantity of alkali activators to be compatible with calcined clays, which are expected to become the primary supplementary cementitious material (SCM) for this technology. So, there is a strong consensus that AACMs aren’t a silver bullet and are not worth pursuing.
The use of digital tools should help improve the efficiencies of our concrete mixes and lead to material production. For example, installing sensors in concrete pours can provide data to create feedback loops and optimise mixes. Inserting chips into concrete mixes could potentially enable an in-situ digital material passport, which further helps with the circular economy in future, reducing demand for new concrete and waste.
So what does the future of concrete look like?
All combined, I see a medium-term future where calcined clays and limestone fines are used as the main SCMs in countries that have transitioned away from fossil fuels, such as the UK, whilst GGBS and fly ash continue to be used where it is locally available. Graphene and digital tools may be used to find efficiencies and reduce total usage, which would enable a faster transition to net zero. In the longer term, emissions from Portland cement will have to be captured, or technologies utilising olivine will be required.
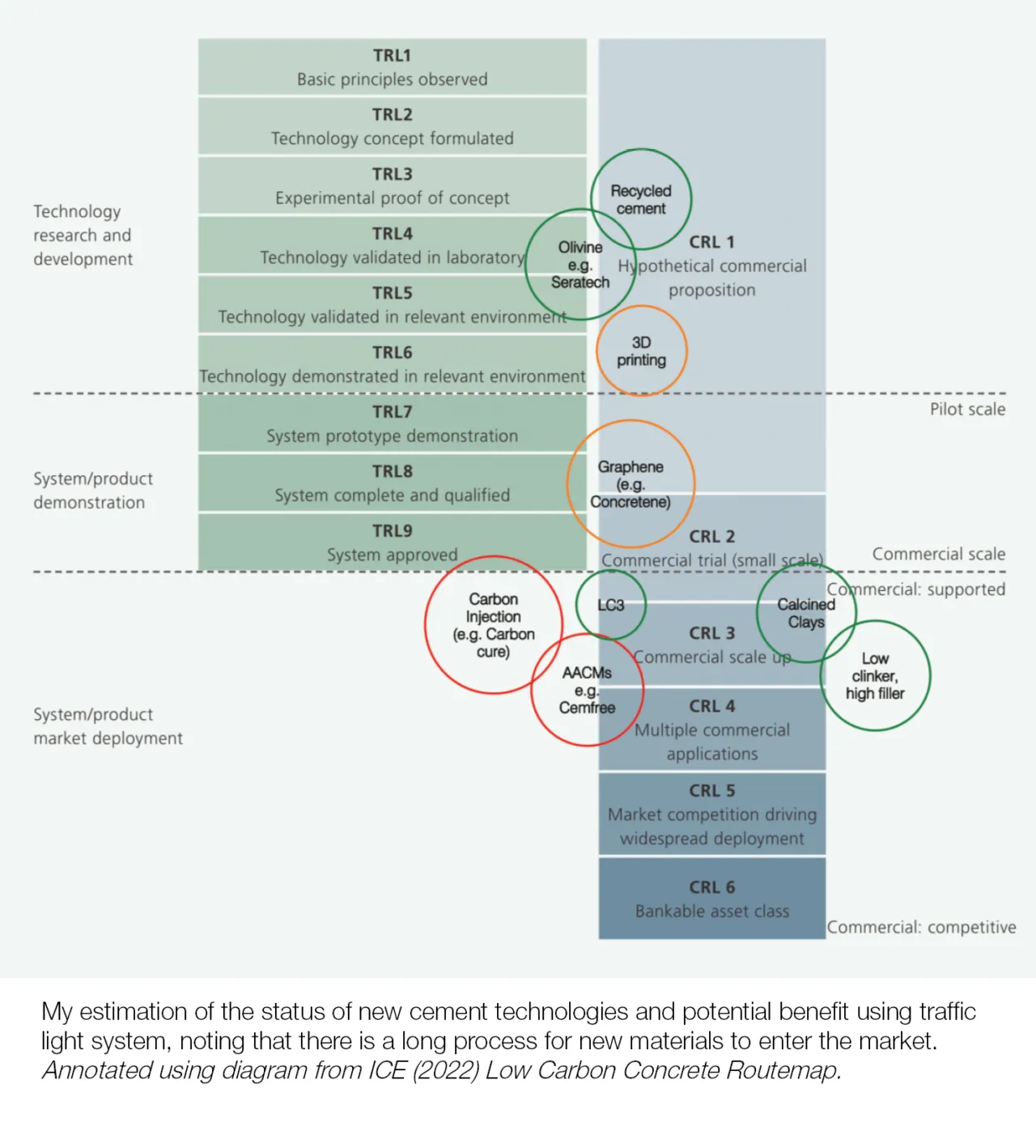
Addressing Concerns and Exploring Further
I’m concerned about the use of branding to greenwash standard market solutions. For example, the Ecopact brand utilises fly ash or GGBS, which are finite resources linked to fossil fuels which are already widely used in the industry. Therefore, I question the effectiveness of such solutions in driving meaningful outcomes.
During my visit, there was minimal discussion about measures to foster a circular economy. We should be considering how to make concrete more deconstructible, changing production methods to facilitate easier upcycling and re-use of constituents at end of life, and developing a business model that provides material as a service. These shifts would incentivise a circular economy, reduce material consumption, and align with a regenerative future.
The concrete industry heavily relies on Carbon Capture, Utilisation, and Storage (CCUS) in current decarbonisation plans. This could be damaging for the industry due to economic reasons outlined above, but it also offers very little societal or environmental benefits beyond decarbonisation. Redirecting investment towards more regenerative materials could potentially yield greater benefits aligned with a positive future.
There is a profound lag in innovation within the construction industry compared to other sectors. Despite contributing similar amounts of global carbon emissions, the construction industry receives significantly less climate technology investment than mobility. To achieve true decarbonisation and regeneration, we need to attract more investment and foster greater innovation within the industry.