Four Reasons Why Specifying Recycled Steel is not a Silver Bullet
24.09.2020
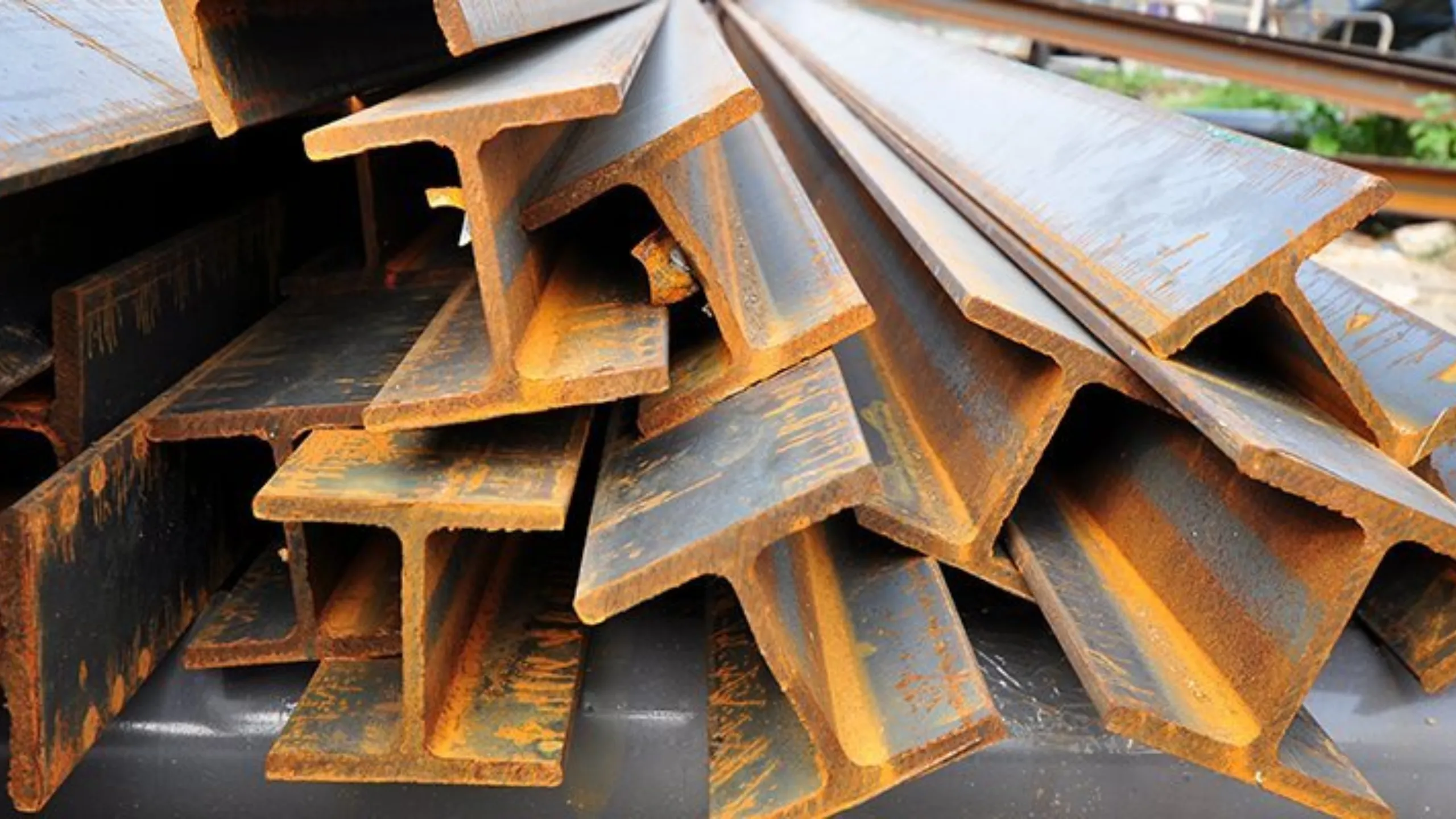
On the face of it, specifying recycled steel for a new build steel frame project would seem to be a ‘no brainer’ to reduce the embodied carbon in the structure and make a positive contribution towards addressing the climate emergency.
Primary steelmaking, with up to 25% recycled scrap steel, in a Basic Oxygen Furnace (BOF) generates 2.3tCO2 per ton of steel. Secondary steelmaking using 100% recycled scrap steel requires an Electric Arc Furnace (EAF) that generates just 0.4tCO2 per ton of steel. Furthermore, with zero carbon electricity serving an EAF plant, nearly all emissions from steel making can be eliminated to 0.1tCO2 per ton of steel.
But there are four clear reasons why specifying recycled steel will not have the impact we think it might
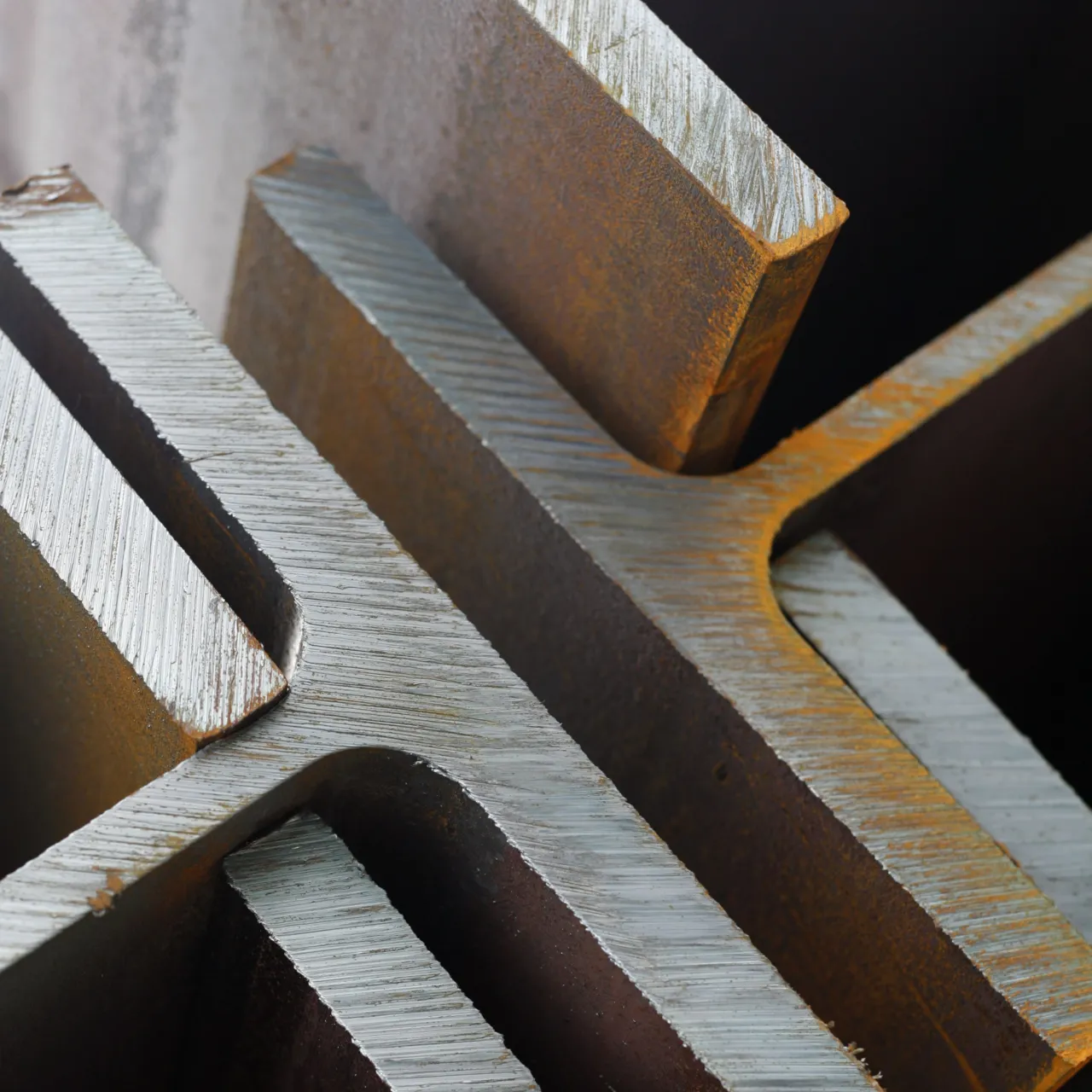
Four reasons why specifying recycled steel is not a silver bullet
The quantity of recycled steel available today is only sufficient to supply around 30% of total steel demand. Therefore, globally we must produce virgin steel to satisfy demand.
Currently there are no EAF plants that produce structural steel sections in the UK (UB, UC & hollow sections). This means any recycled steel must come from Europe so embodied carbon due to transportation to a UK site must be accounted for (lifecycle stage A4). This may still mean the European steel is less carbon intensive but what about the socio-economic impact of not supporting the UK steel industry and UK jobs?
French EAF plants running on green nuclear energy will be significantly more carbon efficient than German EAF plants using dirty coal fired electricity networks.
Without GGBS we have very few options for reducing the carbon content of structural concrete. The two industries are co-dependent.
Re-use of materials in their current state rather than specifying new e.g. existing steel sections, is the best way to minimise embodied carbon but this relies on an effective secondhand market for construction materials which doesn’t exist yet. We know it doesn’t exist because we’re trying to make it happen on our Sunderland project. In the absence of a secondhand market, efficient design and minimising material use is the biggest impact structural engineers can have in reducing demand for steel and thereby reducing its carbon footprint.
Further to this we need to understand the global steel market and material supply chains better so we can specify steel from cleaner or more local sources to direct funds towards the cleanest and most proactive steel producers. Responsible Steel is a not for profit organisation working towards improving the sustainability and responsible sourcing in the steel industry.
Demand for steel will not go away, it’s the world’s largest materials industry, four times bigger than the cement industry. There are several technology routes in development that could enable near zero carbon emissions in steel production such as hydrogen-based direct reduction of iron, carbon capture usage and storage (CCUS), energy efficiency gains and steel production using low carbon electricity. However, these are some way off being commercially viable and having a direct impact on the industry.
In the meantime, structural engineers must design efficiently, set ambitious utilisation targets, design for realistic loadings and avoid secondary steelwork, shelf angles and masonry support angles wherever possible – simple is best!
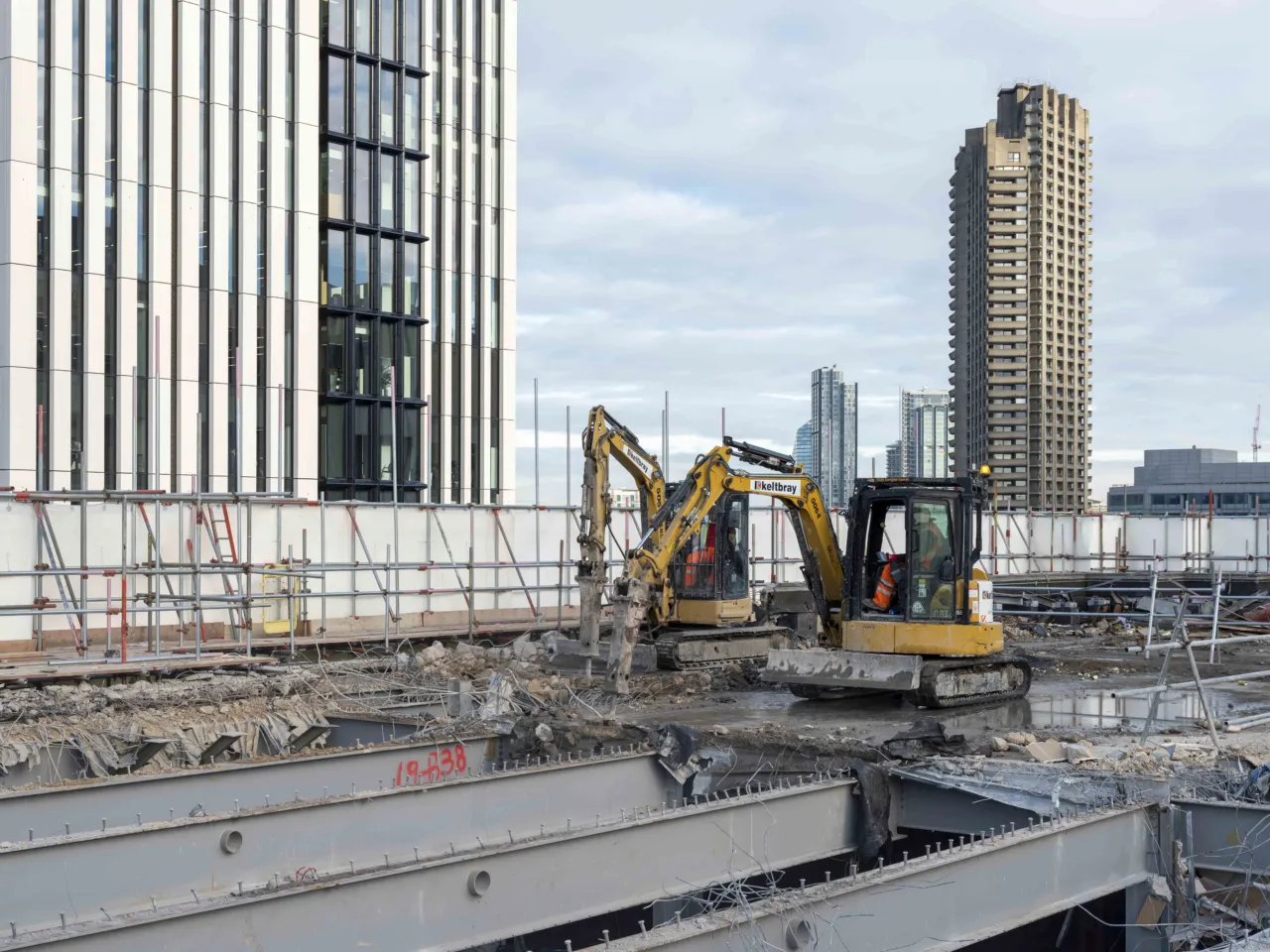