Rammed Earth – Engineering, Sustainability and Craft
04.10.2018
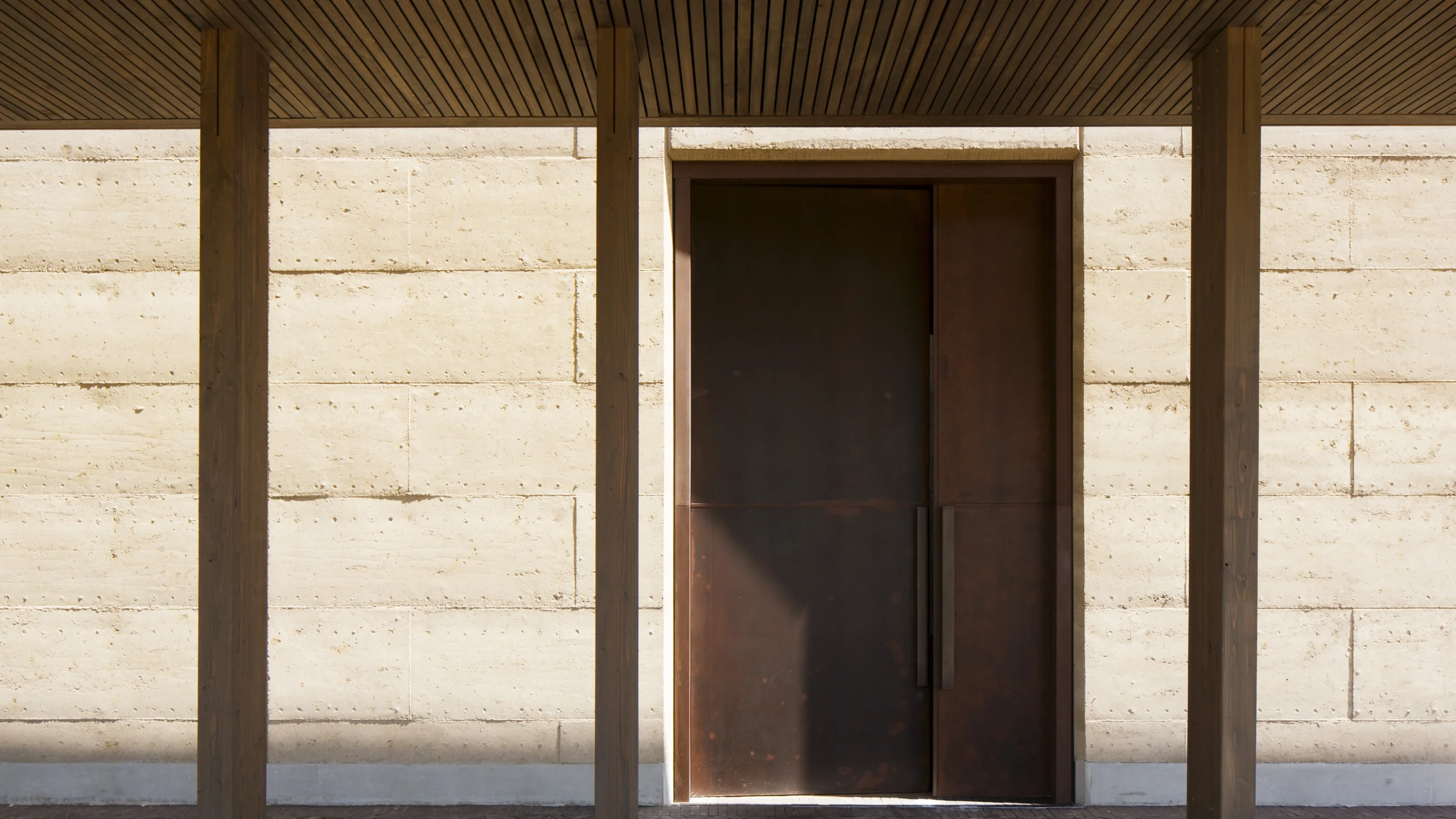
Utilising earth from the site via an ancient, sustainable and durable building method
Bushey Cemetery, opened over 50 years ago, is among the UK's most significant Jewish cemeteries.
The Elliott Wood structural engineers worked closely with the Waugh Thistleton architects and the United Synagogue to deliver the two new simple yet striking prayer halls along with a series of service buildings, across 16 acres of land. The extension has increased the capacity of the site from 43,000 to 60,000 graves, part of an ongoing process of further develop the cemetery for the community to continue to honour and remember those who have passed away.
As a construction technique, rammed earth has been used for centuries around the world, however it is relatively unused and unknown in the UK. It consists of compacting, or ‘ramming’, a moistened mixture of soils into a formwork which, when dried, forms a dense, monolithic wall. Adding lime or cement into the mix improves strength and durability over time - this is known as Stabilised Rammed Earth (SRE).
To construct the seven-metre-high and half-a-metre thick ceremonial walls at Bushey Cemetery, the civil and structural engineers at Elliott Wood worked with Earth Structures, an Australian rammed earth construction specialist firm. The early involvement of specialists meant that any potential drawbacks of the material or construction process could be addressed. Given that there is no official design standard for rammed earth, the engineering team had to justify the proposed design through very thorough repeat testing. Strength, durability, colour and texture were explored to provide a bespoke solution for the project.
Choosing the correct soil mix is crucial to the success of the technique. The aim of the mix, combined with the compaction method, is generally to maximise the resulting dry density of the wall, and therefore its strength and durability.
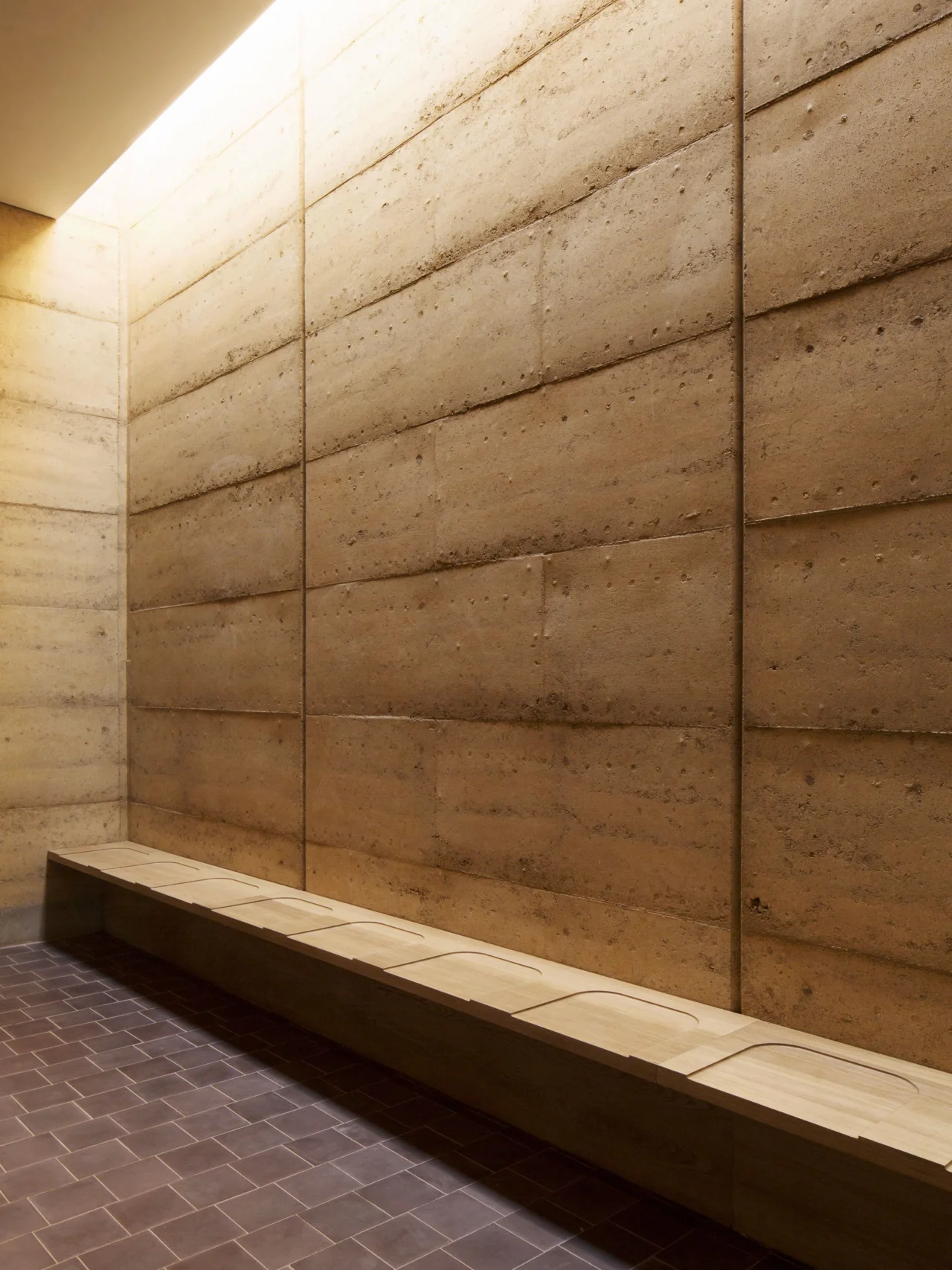
Key constituents of the mix
Soils are classified based on their particle size, with clay having the smallest particles, increasing through silts, sands and then gravels. Sands and gravels make up the largest proportion of the soil mix, generally 50-80%, and the maximum particle size for rammed earth is generally limited to 20mm (medium gravel).
The type of binder used affects the proportion of clay that is acceptable. In unstabilised rammed earth, a higher clay content is used to act as the binding agent. Clays with lower plasticity are preferred to avoid excessive shrinkage during the drying of the structure. When exposed to moisture, however, the binding effect of the clay is lost, as the material loses its strength and becomes susceptible to erosion. This is only suitable for arid areas, otherwise requiring coatings and regular maintenance.
Where lime or cement is added to form SRE, the clay content is reduced while the sand and gravel content is increased to ensure the water in the mix is available for hydration. A cement content of around 7% by weight is typical, less than half the proportion generally used in concrete.
A particular mix will have an optimum water content that is dependent on the method of compaction and which maximises the dry density. For SRE, the water content is typically 7-10% and is judged by “adding water until the mix will hold together when squeezed in the hand - but not leave a colour stain on the hand”. It is important that the water contains minimal salt and organic matter.
A plasticising additive reduces the water absorption of the finished wall, as well as increasing its strength by improving workability at lower water contents.
At Bushey Cemetery, the scale of the 7m high walls, and the desire to keep much of the rammed earth walls exposed to the elements meant that cement SRE was chosen.
Testing the Rammed Earth Mix
Our Approach
Finalisation
Within the ceremonial spaces of the prayer halls, the rammed earth has been left exposed, showing its inherent imperfections and giving the space a unique character. Different shades of the materials are visible in the stratification across its surface, and the 150mm layers of ramming sections can be seen as well, adding to the bare yet elegant aesthetic. While this external façade is solemn and austere, once inside the atmosphere is calm, inviting yet private, softened further by the use of timber and indirect soft light.
Unlike a perfectly poured and polished concrete wall, the rammed earth technique gives the Bushey Cemetery and Prayer Halls a unique character, a sense of sombre, calm beauty. Another plus of using this material is the noise attenuation effect, which amplifies the tranquil yet solemn atmosphere required by funeral ceremonies.
The use of rammed earth comes with strong sustainability credentials, including the time and cost efficiency of locally sourcing the raw materials and its manual construction methods. It uses significantly fewer natural resources than fired bricks or concrete walling. The material is also breathable and has a temperature stabilising effect. Given this and considering that the buildings were designed as sheltered external spaces, no insulation was required in addition to the material’s inherent high degree of thermal mass. The technique is likely to become increasingly popular and important for low carbon building.
The rammed earth walls designed by the Elliott Wood team reflect the makers’ craft in building them, utilising locally sourced materials through an ancient, sustainable and durable building method. Echoing the return to earth of the body, once all these new graves have been taken and the halls are no longer needed, the structures above ground have been carefully specified to be demounted and recycled, returning to the ground from which they came from, a fitting parallel to the human condition.
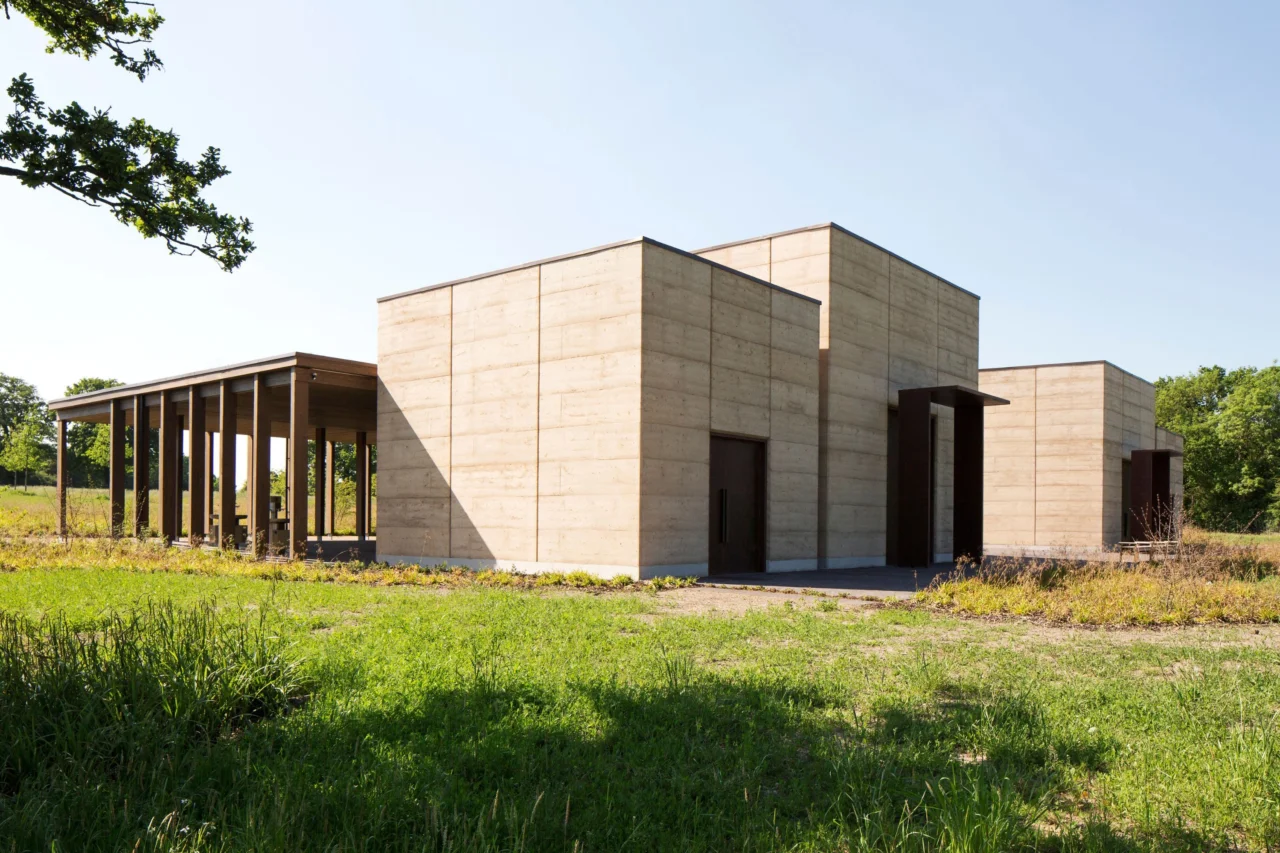